Presentado por: Ing. Agr. Jorgelina Lezaun
Agribusiness & Marketing Consultant
jorgelina.lezaun@gmail.com
October 2024
Most phytosanitary products are designed to be diluted in water -as a vehicle- and used or sprayed alone, but they are mixed to achieve different objectives such as:
|
The diversity of formulations of phytosanitary products requires different handling and agitation needs within the spray solution, as there is also differential compatibility between the components of the mixture.
The variables at the time of combining them generate different situations in which the products are not always compatible for mixing.
There are statistics where the “mixing errors” factor constitutes 33% of application failures (R. Wolff, 2001).
|
The “mixture” results that affect control effectiveness can be:
The order in which the mixtures are prepared in the tank depends on the formulation and NOT on the type of product (herbicide, fungicide or insecticide). To achieve the effectiveness of the mixture, it is necessary to respect an order that ensures that the soluble matter dissolves first.
It should be noted that soluble products (liquid, granulated or powder) do not separate into phases and do not require agitation, which is why they always come first, after water conditioners if they need to be used.
The correct mixing order is:
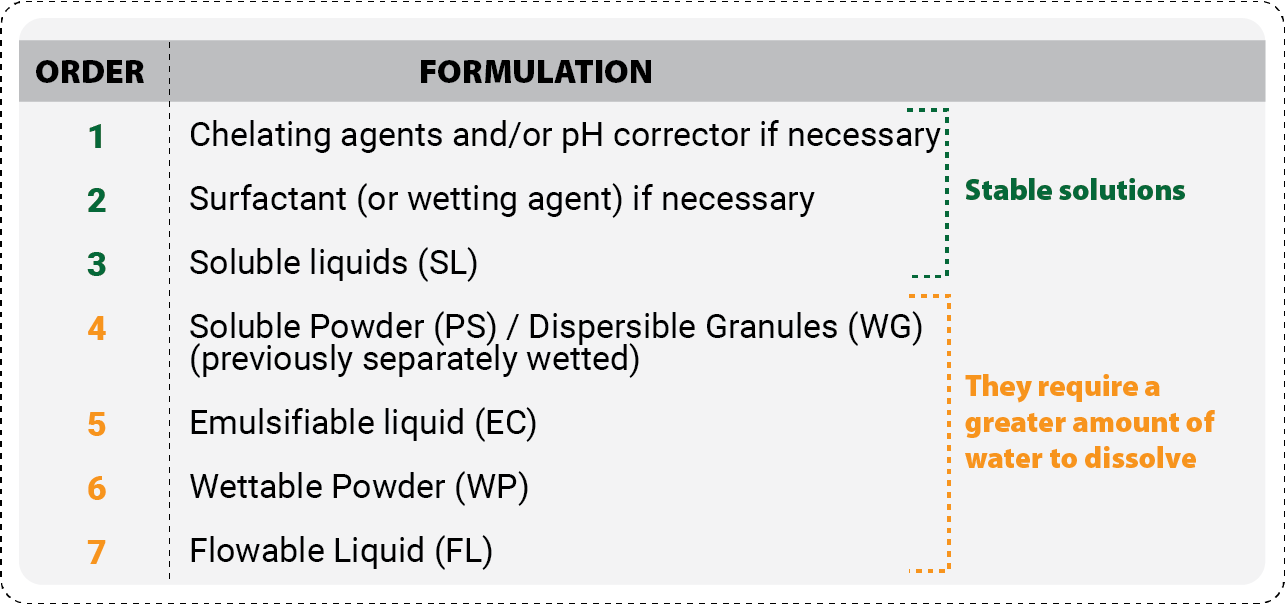
The compatibility test is the best tool to decide the mixing order of different agrochemicals, since there are a large number of formulations with different characteristics and commercial quality. In addition, the quality of the water (salts, hardness, pH), environmental conditions such as temperature and the operating efficiency of the sprayer's agitation system, which will influence the application results, are not always known.
It is advisable to carry out a small-scale compatibility test and test the order in which pesticides are added to the tank. The test must be carried out respecting the proportion of products to be used in the field, water conditions and the environment in which the application will be made.
It should be noted that the “soluble” do not separate into phases and are therefore incorporated first into the test.
It is worth noting that only the active ingredient is mentioned on the labels, and information on mixtures is scarce, making it difficult to estimate the result of a mixture.
The manufacturer guarantees the product used alone or for the mixtures detailed on the label and clarifies any known incompatibilities.
Compatibility test
- In a container (preferably glass), a mixture is made, keeping exactly the same proportion of each of the components in which the application will be made.
- Proceed by adding one product at a time to 100 cc of water, stir and top up with water to 200 cc. Then shake by inverting the closed container up to 10 times, observe and observe again after 30 minutes.
- Recommendations will emerge based on the results:
Types of mix
The results of the compatibility test allow a clear differentiation between the types of mixture.
- Compatible Mix: It is a smooth mixture. No distinct phases. If there is any slight sediment, it dissolves immediately when shaken. The products can be used together.
- Incompatible mixture: has a lumpy or flocculent appearance. If shaken, the components do not dissolve, or they separate again immediately.
In some cases, heat release can be detected, which is an unequivocal sign of chemical reactions between the components. In this case, the use of compatibilizers cannot even be attempted.
The predisposing conditions to the “incompatibility” of a mixture are:
|
Furthermore, it must be considered that the loading operation is a factor that contributes to the aggravation of the problems of mixtures, since incorrectly, many times two or more pure pesticide products are mixed in the loading container.
Emulsifiable formulations and suspensions also require a good agitation system, and the equipment normally depends on a hydraulic return system to perform this function, which is not always well designed and sized.
On the other hand, mixtures of different formulations, with different requirements, emphasize the need to mechanically contribute to the homogenization of the spray solution.
Observations
Adjuvants, spreaders or additives
“An adjuvant is any substance added to the spray tank separately from the pesticide formulation in order to improve pesticide performance” (J. Witt 2012).
Formulations contain inactive ingredients that are used to adapt the active ingredient of the formulation by improving the activity of the product or to facilitate the application process.
Many of them are marketed independently with different functions: anti-foam, pH correctors, anti-drift, surfactants, emulsifiers, penetrants, compatibilizers, etc.
Adjuvants can improve product performance by:
|
According to their main effect of action, adjuvants can be classified as:
-
Activators with action on the leaf surface
1.1 Surfactants – Wetting agents Their function is to reduce the surface tension of the water that acts as a diluent for the agrochemical. They also act as emulsifiers of the oil in the water. Their use aims to achieve the best contact between the product and the leaf (smaller contact angle between the two) by reducing the surface tension.
Source: INTA
Labels may refer to “penetrating” because the larger contact surface may allow for greater penetration of the product. Greater contact with the leaf determines the “wetting” action.
According to Hartzler (2001), surfactants added to the spray solution optimize control of herbicidal action because the greater the number of drops, the greater the contact with the leaf surface, but up to a certain point 0.5% because after that, according to experiences, the excess causes the water to run off, dragging the product along and this would reduce the control as well as cause an unnecessary cost.
Source: INTA (Hartzler 2001).
Surfactants are composed of a molecule consisting of a hydrophobic sector (lipophilic and apolar chain) and another hydrophilic sector (polar).
This molecular structure allows oils/fats to dissolve in water and vice versa. That is, an “emulsion” is formed from 2 immiscible liquids, one in the dispersed phase (water) and the other in the continuous phase (fats/oils).
Conventional surfactants have a mass of 200-300 molecular mass units (amu).
According to their ability to ionize in an aqueous medium, they are classified as:
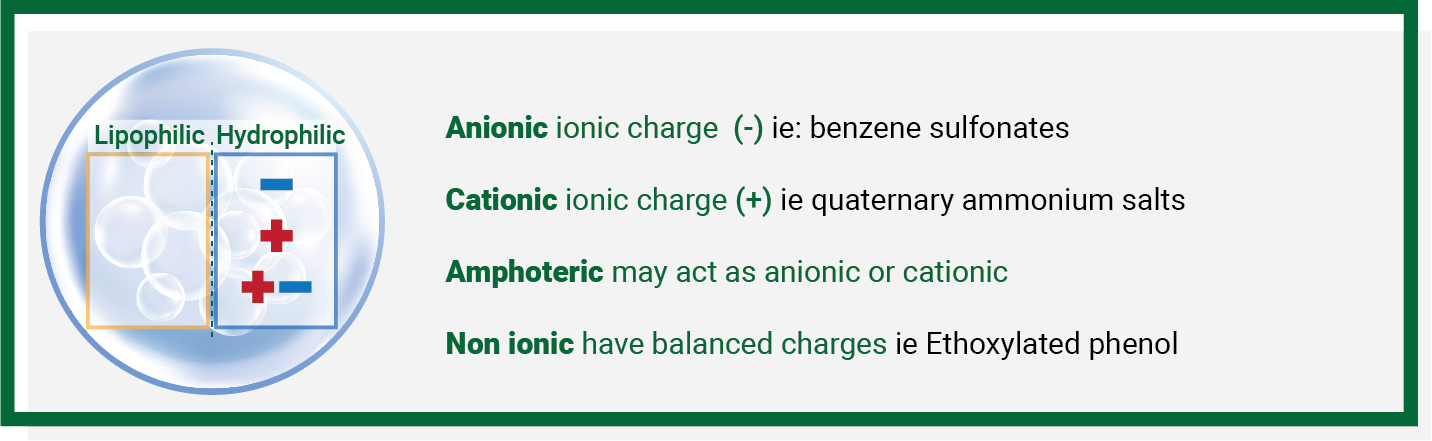
Silicone coated
The advantage of this is that at low doses the surface tension is reduced due to its better location on the leaf. They are composed of silica and silicone. The hydrophobic sector is the silicone body and the ethylene oxide the hydrophilic sector.
Surfactants play a key role in the application of contact products. In some systemic pesticides - which act by phloem translocation - they can also contribute to improving their functioning.
Penetrants
Their function is to ensure that systemic products enter the membranes of the leaf surface to be translocated. This is achieved by greater persistence in the leaf or by their ability to dissolve cuticles and waxy substances.
The wax, cutin and pectin layers of the leaf cuticle are the main barrier to the action of the phytosanitary product. Waxes are lipophilic, which prevents water loss to the outside and also act as a barrier to the entry of hydrophilic products.
Pectin layers are more hydrophilic and act as a barrier to lipophilic herbicides, which is why penetrants are important.
Penetrating agents have the function of altering the cell membrane and dissolving the wax layer of the leaves. The recommended dose should be applied since an excess can cause phytotoxicity or damage to the plant. In products that act by contact, their use does not make much sense.
In addition, penetrants help with temperature variations, as a lack of absorption at low temperatures has been proven (Baur et al 1999).
Penetrating agents can be:
|
Both mineral and vegetable oils perform anti-evaporative functions.
Source: INTA (Ing Leiva)
In an oily medium with the same nozzle and application pressure, the drops are smaller (than in an aqueous medium) due to the lower surface tension of the oil, but as the oil takes longer to evaporate, the water drops with a larger initial size decrease in size.
For this reason, it is recommended not to use oil as an anti-evaporant if the Relative Humidity (RH) of the environment is >60%. In aerial applications the rates should be higher than those on the ground.
1.2 Adherent or Sticker: Their function is to “stick” the product to the leaf. They are latex, resins, plastic polymers with adhesiveness. They are frequently used in tropical areas, with frequent torrential rains that can “wash or drag” the pesticide product.
-
Utilitarian or of specific purpose
2.1 pH correctors/acidifiers
They serve to ensure the effectiveness of a phytosanitary product under adverse water conditions:
- High pH (alkaline): when combined with agrochemicals, alkaline hydrolysis occurs in hydroxyl groups and effectiveness is lost. At higher temperatures and pH of the water, the process accelerates.
- Presence of salts (hard water): If salts are abundant, they combine with agrochemicals, producing compounds that are difficult to absorb.
-
For both reasons it is necessary to correct this situation by lowering the alkalinity (decreasing the pH), that is, by acidifying the medium and/or eliminating or sequestering cations.Correcting agents’ doses depend on the alkalinity and salt content. Phosphoric acid or buffer solutions that maintain an optimal pH range are normally used. Orthophosphoric acid, orthophosphates, hydroxyethanes, etc. are used as sequestrants.
In any case, it is advisable to perform a water analysis before making decisions regarding correctors.
2.2 Anti-drift agents Drift depends on the size of droplets that are exposed to environmental conditions, evaporation and transport by the wind.
-
Any increase in liquid density reduces the droplet size. As the volumetric diameter of the drop increases, drift decreases.
The variation in the density of the liquid affects the flow rate of the nozzle at a given pressure, being lower the higher the density.
An important factor to consider is the solubility of the antidraft agent in water because it can affect nozzles.
Both effects must be taken into account when using products with a density different from water such as liquid fertilizers.
2.3 Compatibilizers are used to mix two products that could not be used together without the adjuvant.
Warning: In the case of two incompatible products - which must be mixed with compatibilizers - they should not be used in the field by the user, only proceed in a laboratory or by formulators so that the active ingredients guarantee their effectiveness and avoid dangers.
Annexes
1-Summary of formulations Source: INTA Pergamino Agr. PD LEIVA - Nov 2013
2-Comparison of formulations:
Sources:
- org/en/news/ristóbal/i-do-read-labels-and-safety-sheets-of-phytosanitary-products
- Inta-Good Practices for the application of phytosanitary products / Brambilla V. Gómez Hermida M. Bogliani
- World Health Organization (WHO) 1992 – Health consequences of the use of pesticides in agriculture. Geneva. Switzerland – 128 pp.
- SENASA Argentina Applicators Manual
- INTA Efficient application of phytosanitary products
- FAO Manual on the preparation of pesticides
- CASAFE Manual for Responsible Use of Phytosanitary Products 2020
- INTA Pergamino Pesticide formulation Agr. Eng. Pedro Daniel LEIVA Nov 2013
- INTA Pergamino Tank Mixtures and Compatibility Tests Agr. Eng. Pedro Daniel LEIVA
- University of Comahue Argentina Formulations Prof.HU Gentile
- Formulations and mixtures of phytosanitary products in agricultural risk ristobal colon auria chemical engineer iqs
- Chacra Magazine Note 10787 Mixture of phytosanitary products
- Bulletin of Disclosure N°41 ISSN 0328-3380 Guide for the proper use of pesticides and the correct disposal of their containers Agr. Eng. Fanny Martens INTA - Rural Extension Agency Tandil
- Water quality and mixtures of phytosanitary products 2015 Agr. Eng. ( M.Sc .) Juan P. Renzi